1.导轨结合面尺寸设计
机床导轨非常重要,其精度不仅影响机床整体性能,还与支撑件有很大关联,所以机床导轨与机床性能密不可分。导轨的组成可以分为安装面、导轨和移动构件3 个方面。导轨是实现支撑、导向和运动的部件,移动件是安装在导轨顶面的运动部件,如图1 所示。
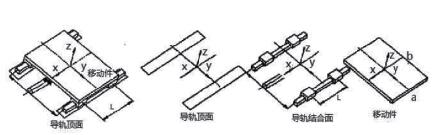
图1 导轨结构示意图
传统导轨的设计原则如下:
(1)机床的最大加工直径决定导轨之间的跨距,导轨的跨距越小,导轨的接触面受力越大,缺点是会使床鞍产生倾覆角。
(2)导轨的跨距受机床整体外形尺寸的限制,床鞍的刚度也会受到影响。
(3)机床导轨尺寸设计出一个范围,后期再根据设计人员优化进行尺寸设计。
导轨系统设计后需要对其进行优化,优化方法是对机床导轨系统进行三维模拟建模。建模的方法是模拟机床导轨系统,将移动件、导轨、导轨底面进行模拟,优化设置分为优化目标、优化约束、设计变量3 个方面。
(1)优化目标。导轨的优化目标是将导轨的最小柔度作为变量,也可以将导轨移动件顶面中心的最大变量作为优化目标。
(2)优化约束。约束是导轨结合面体积分数要小于优化后的。
(3)设计变量。将导轨结合面的单位密度作为设计变量。
2.床身导轨尺寸设计
根据机床导轨的性能和尺寸设计一套机床床身导轨的设计流程,如图2 所示:
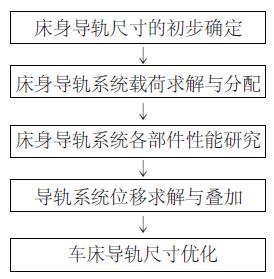
图2 床身导轨尺寸设计流程
(1)床身导轨尺寸的初步确定不能根据设计者的意愿进行设计,需要根据以往传统设计方法对床身导轨进行初步确定。
(2)床身导轨系统载荷求解与分配。机床在工作过程中,由于零件与机床之间的相对运动,机床本身的载荷是非常复杂的,而机床导轨的载荷采用机床常规工况下的载荷作为研究对象,也就是机床的切削参数,将机床切削时的载荷分配到机床导轨上,将切削参数产生的3 个力分配到机床导轨上之后,根据静力平衡原理,再将载荷等效地分配到导轨系统的3 个组成部分上,最终求得导轨每个部件所受的力。
根据上述理论进行距离说明,利用斜床身车床进行载荷分析计算,斜床身车床是两轴联动机床,床身为45°结构形式,具有载荷强,吸震性好的优点,如图3 所示:
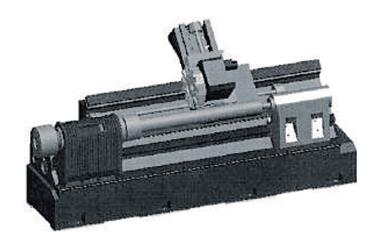
图3 斜床身车床三维示意图
根据机床的使用情况,选取床身连接主轴、床鞍、尾座时的受力载荷,滑板、床鞍与刀架连接所受的载荷,主轴箱、尾座与主轴以及尾座套之间的载荷,选取这3 处工况进行载荷分析。利用功率法求切削力,计算公式如下:
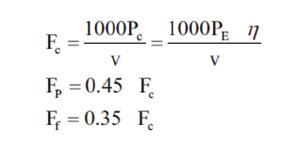
式中, F c、F P、F f 为主切削力、背向力和进给切削力;PE、Pc 为主轴电机功率和切削功率;η 为能量传递效率;v 为切削速度。
(3)床身导轨系统各部件性能研究。对导轨的3 个组成部分进行结构形式和刚度特性研究。
(4)床身导轨系统位移求解与叠加。根据上边各个部件载荷分布与大小,再结合机床导轨的整体刚度特性,将导轨在工作过程中各部件位移情况进行求解,图4为导轨系统位移的一种形式。
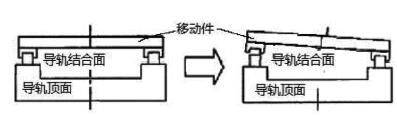
图4 床身导轨位移示意图
床身导轨系统在不受载荷情况下,各个零件部件处于相对理想位置,通过对各部件建立坐标系,会发现坐标系的原点会在一条直线上,但是床身导轨在受到外载荷作用时,坐标系会发生变化,而各部件也会发生位移。
对床身导轨每个部件的坐标系进行分解,会求解出坐标系矢量叠加后在一个方向上,这个方向就是部件位移方向,通过导轨系统位移叠加最终求得导轨系统位移优化方向。
( 5 ) 床身导轨系统尺寸优化。尺寸优化是消除各部件之间的影响,利用模型最终确定合理尺寸特征,分别通过结构件相对性能和约束,再通过尺寸作为变量,对机床导轨进行优化,优化时将导轨尺寸进行重新计算,选择合理结构进行检验,最终确定符合实际的尺寸,确定机床导轨的零件图。
3.床身结构设计
导轨结构设计的流程为: 确定设计指标、建立物理模型、概念设计、结构方案设计、尺寸优化、性能分析与评价、方案确定。
3.1床身结构的设计指标
为了保证机床加工的精度,机床导轨的基本设计指标要满足强度高、静态刚度高、使用寿命长等要求。在设计一些大型或结构件质量大的机床时,质量应作为机床设计的指标; 但是在一些基本指标相同的情况下,质量又小的时候,很难找到设计指标,这时导轨的设计可以根据机床的刚度和材料等指标; 有的机床在设计时需根据客户进行特定设计。
3.2机床结构物理建模
主要的结构建模为几何建模、载荷求解、约束等效和设定材料属性等。几何建模包括数字化建模和基础优化初始建模,后者的建模包括轴承、丝杠等零件的建模,载荷求解是对床身导轨系统的载荷计算,载荷主要是由主轴箱、尾座、床鞍等部件产生的,载荷求解是根据静力平衡方程。约束等效是机床床身上的部件与其配合或者相邻构件之间的连接,它们之间会产生一种相互之间的约束。这些约束等效形式的合力会影响床身导轨的精度。设定材料属性是基于机床构件各自的功能要求,根据机床床身结构件材料的实际特性进行优化,如螺纹材料的钢、床身本体的铸钢。
3.3 床身概念模型设计
概念模型就是利用床身拓扑优化设计寻找最优传递路径,床身拓扑优化有限元模型的建立是通过建立优化区域和非优化区域,设定工况载荷、约束、工艺性能等参数,完成优化模型处理后对床身进行六面体网格划分,对床身进行结构优化,目的是利用较少的材料满足机床的设计要求和性能,降低制造成本。
3.4 床身构型方案设计
床身构型方案设计是对初始提出的模糊设计模型,不具备制造工艺的方案进行工艺上的合理设计,因此在床身设计方案的确定上需要人工修正。床身构型可以分为外部壁板、内部壁板、主筋板三种模型设计。
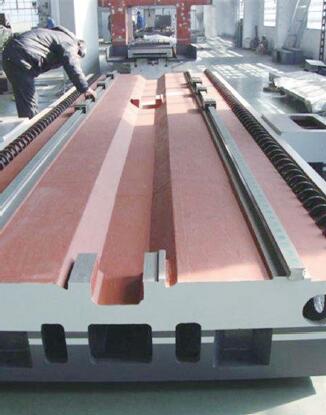
3.5 床身尺寸优化
尺寸优化是利用有限元软件对床身进行性能参数与特征尺寸数据处理,常用的软件为ANSYS 模块workbench。
3.6 床身性能分析
将床身性能分析参数作为性能分析与评价的依据,再建立床身性能分析模型,最后根据床身的性能分析结构对比优化前后床身本身发生的变化,包括床身的质量、静刚度等,最终得到床身优化分析的结果,评价出较为合理的结构方案。在机床床身优化前后对比中,优化后的指标一定会比之前好。通过静刚度的对比,会发现床身的X 方向或Y 方向上的刚度会比优化前有所提高。机床质量的优化是一个很重要的指标,不仅会节省机床生产材料,还会降低能耗,达到节约成本的目的。
4.结语
机床导轨的精度关系到整体机床的性能,而导轨的设计是导轨精度的前提。如何在导轨结合面接触形式不改变的前提下,保证导轨的接触长度改变,从而使机床性能达到最优是关键。现代机床导轨的设计,可以使用机床载荷力学模型,分析机床床身的载荷,求解机床导轨的受力情况,设计出精度高的导轨。但是,单一地提高机床导轨的性能,还不能有效提高机床整体性能。机床是一个整体,只有将机床的每个零件充分优化,才能有效提高机床性能。
折至功能部件网